The e-tronsformers: shapers of change
Ingolstadt is ready for its first all-electric model: the Audi Q6 e-tron. New skills are required for this. Over 8,300 employees from Production, Technical Development and Sales have therefore undergone further training - and are boldly breaking new ground in the world of electric mobility. Seven examples.
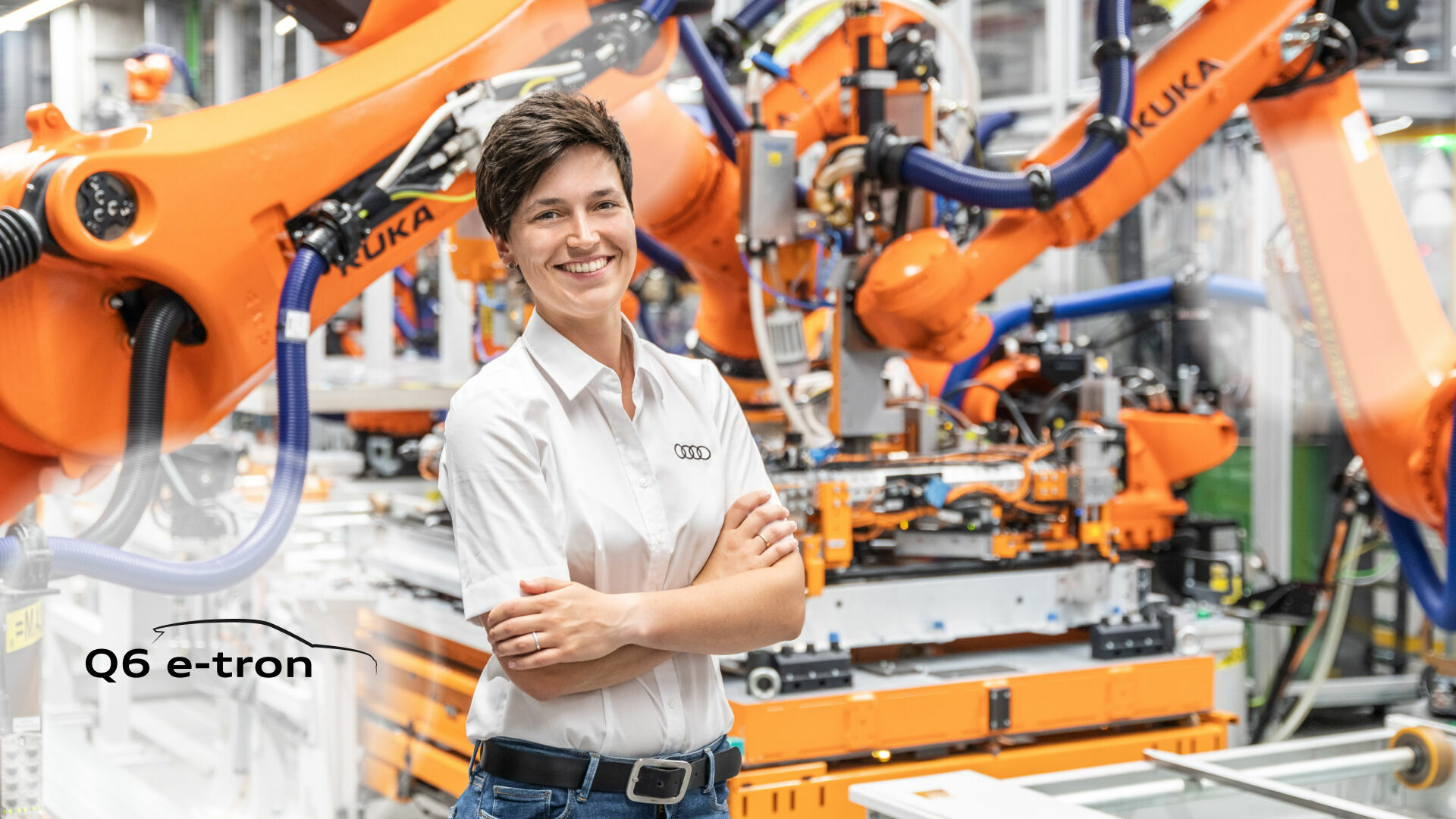
Maria Salbeck switches to battery assembly
At Audi's headquarters in Ingolstadt, 27-year-old Maria Salbeck has decided to switch to electric mobility. The trained mechatronics technician for automation technology has undergone further training to become an expert in new battery assembly. She previously worked in the paint shop as a plant operator and at the Audi Training Center as a co-trainer. "Then I wanted to get back into production, back to the product," says Salbeck.
She is now responsible for a wide range of battery assembly technologies and oversees an entire assembly line section. It is a step she does not regret. "If you want to, you have the opportunity to try out a lot of things at Audi and to develop personally," says Salbeck. "Sometimes you have to take a more difficult path and dare to jump in at the deep end." Salbeck's recipe for success is approaching each other and working together openly and closely as a team.
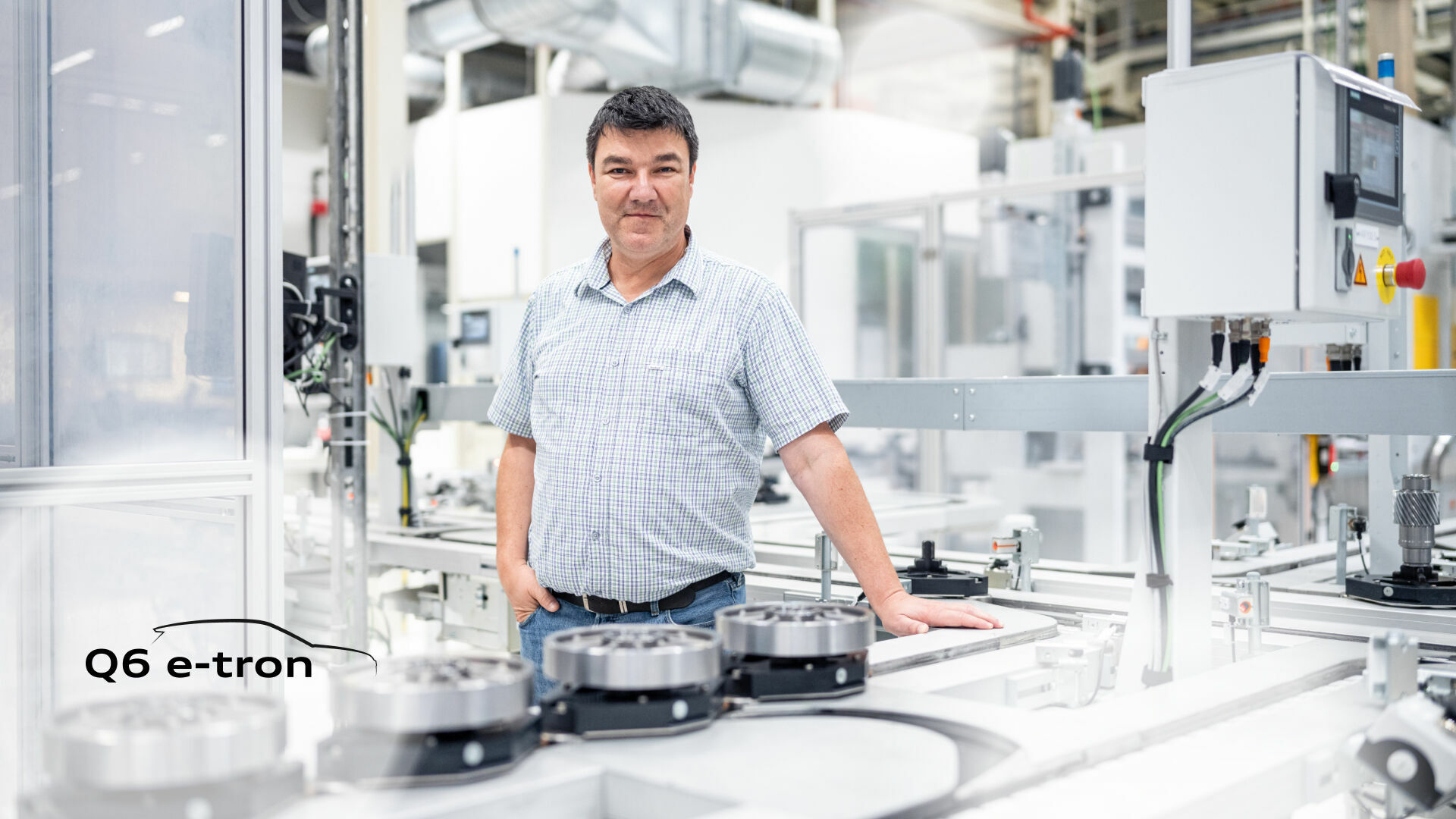
Attila Kovacs plans drive systems for the Premium Platform Electric
Attila Kovacs has worked at Audi for 25 years. In 2019, he switched from combustion engines to electric drives within Production Planning at Audi Hungaria in Győr. For Kovacs, switching to e-mobility was a pragmatic decision: "This technology will take on a leading role in the future. I want to play my part in this."
Following series production of the Audi e-tron motor, since 2021, he and his team have been planning the drives for the Premium Platform Electric (PPE), on which the new Audi Q6 e-tron series, for example, is based. "It makes me proud to be involved in this important technology," says Kovacs, who has no regrets about his move within the company. "Reinventing yourself from time to time gives you a fresh head and new motivation."
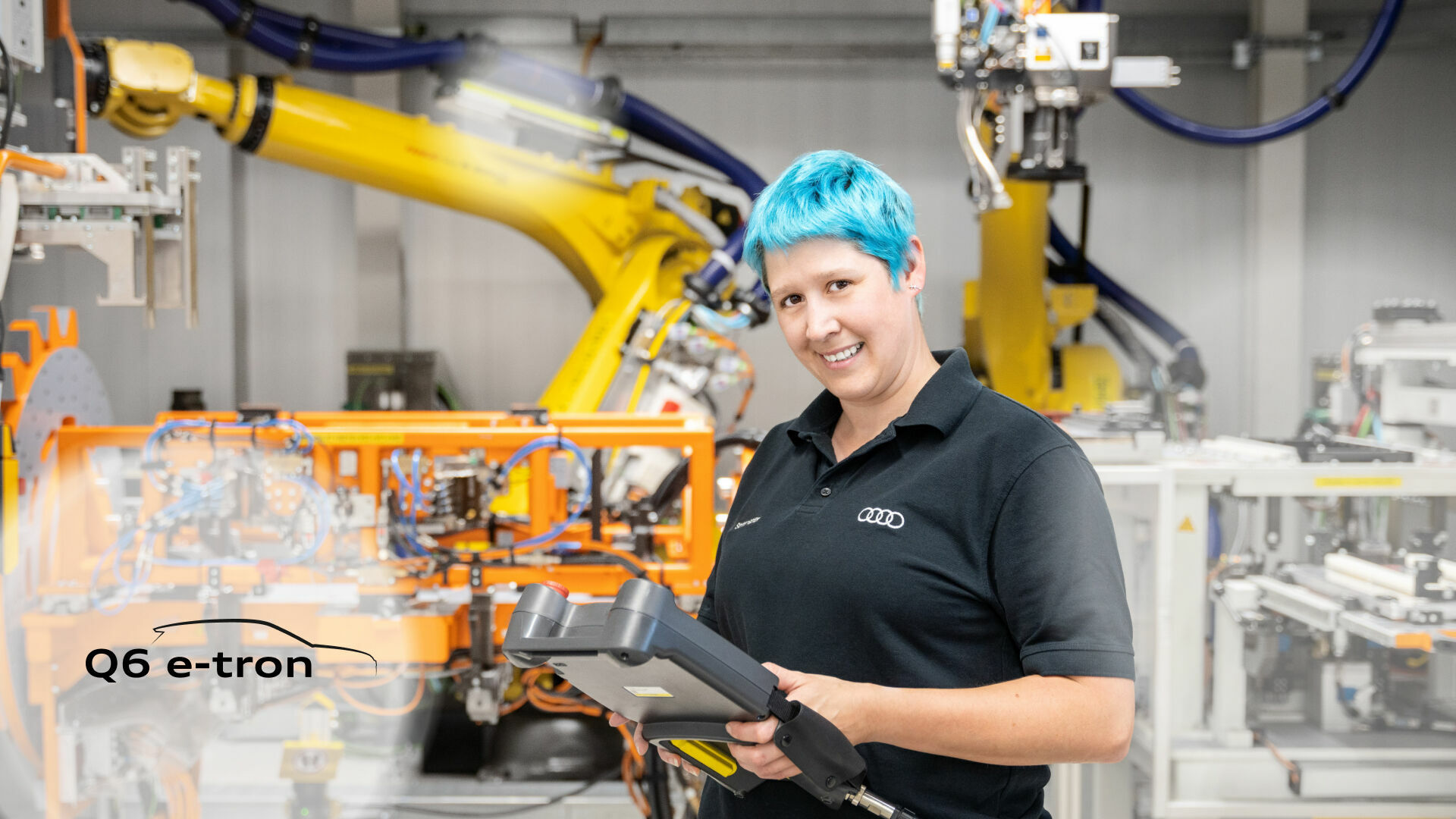
Stefanie Strittmatter is a pioneer in battery production
Stefanie Strittmatter was among the first of six employees to start working in battery production in 2020 - and reinvented herself to do so. After 16 years with the company in various positions, the trained electronics technician for automation technology decided to look for a new challenge - and trained for a job in battery production. Strittmatter reflects: "It was fascinating to see how battery production was created from scratch."
Now, Strittmatter specializes in Audi's module production. Here, the employee for the four rings assembles battery modules almost entirely independently, with only the battery cells coming from suppliers. She is particularly fascinated by how the robots work alongside her team. "Learning and growing together has helped bond our team," says Strittmatter. This spirit drives her on again and again.
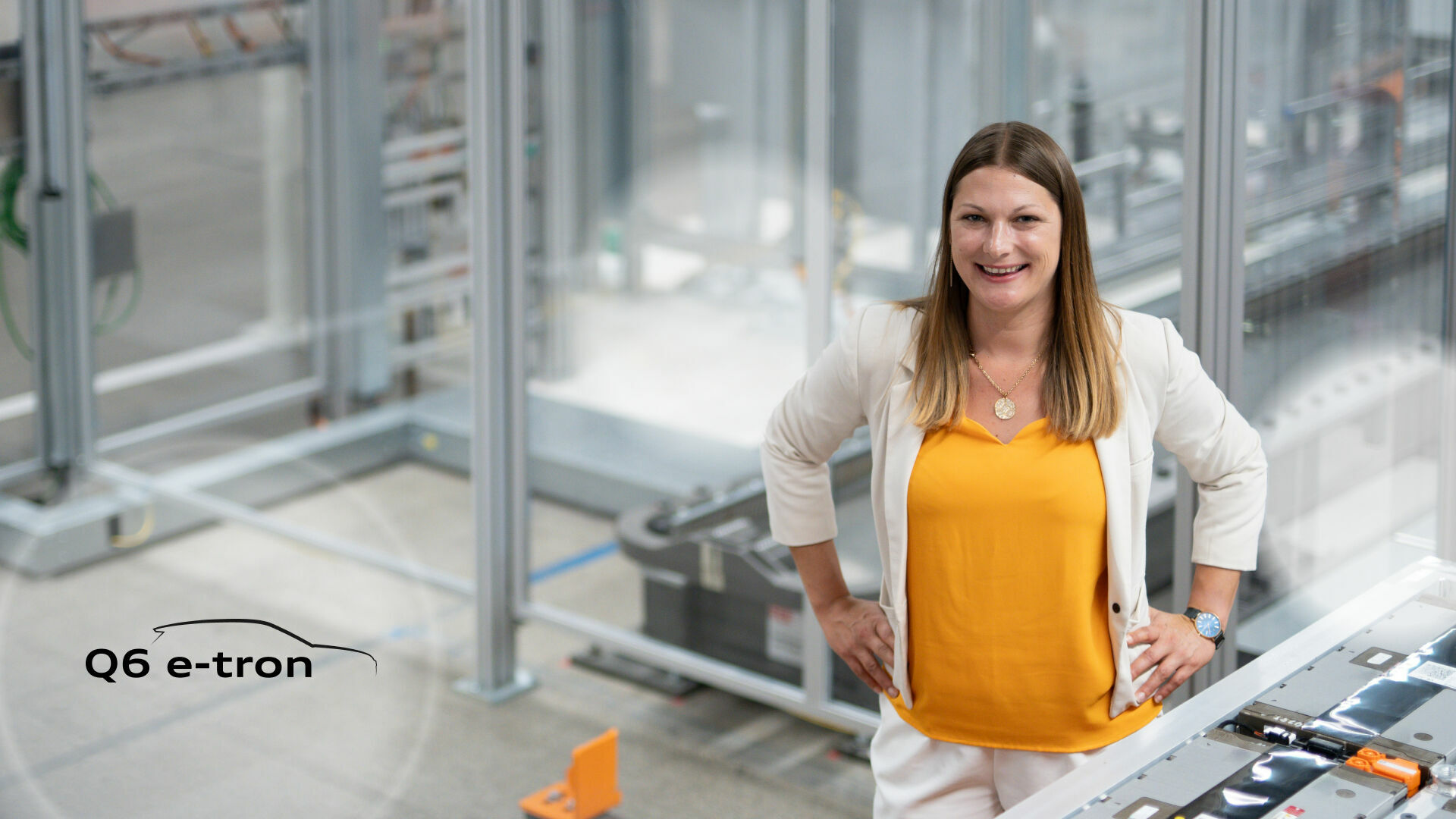
Katja Wagenpfeil has been passionate about battery systems since the very beginning
Katja Wagenpfeil knows e-mobility at Audi like the back of her hand. "The Audi e-tron is basically my baby," she says. Originally responsible for procuring engine components, she was part of the team that set up a multi-supplier strategy for components for high-voltage battery systems in 2013. "From this period onwards, many projects developed in the direction of e-mobility," recalls Wagenpfeil, who later took over project management of the high-voltage battery for the Audi e-tron, responsible for managing the PPE high-voltage battery system's technology, quality, and costs. Wagenpfeil also worked in battery cell development at Volkswagen for two years.
Today, the business administration graduate is the team leader responsible for the transmissions of all-electric vehicles. "Colleagues’ interest and motivation to switch to e-mobility grow constantly. Changes of perspective and department are possible at Audi at any time - and desired."
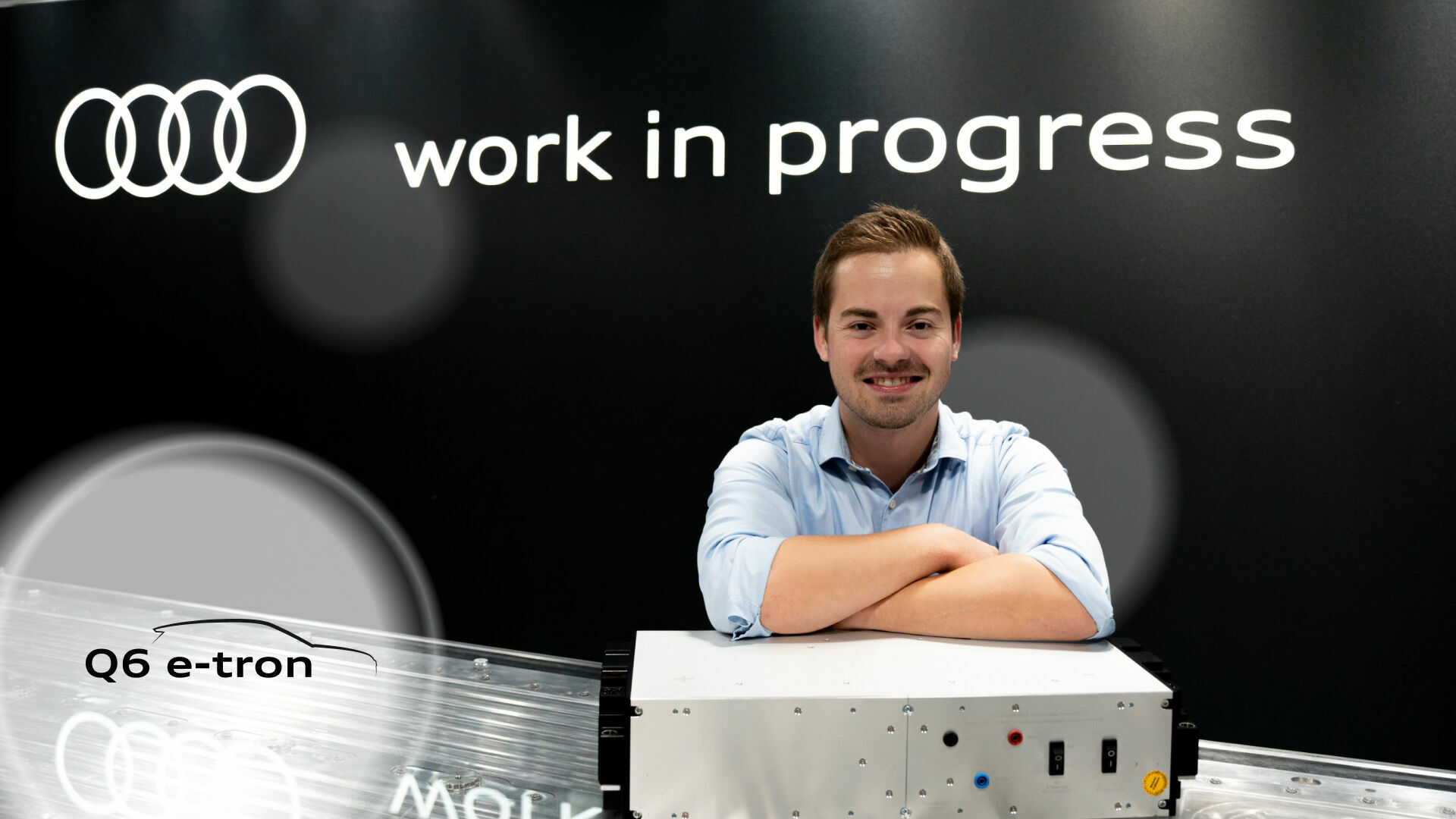
Markus Kammerbauer develops processes for handling high-voltages
It is the pioneering approach and team spirit that fascinates Markus Kammerbauer so much about his work at Audi. "We are a small team; everyone can rely on each other. And we have the chance to shape the future with our work," says the 28-year-old. Kammerbauer works in Ingolstadt as an electrical specialist in the High-voltage system production planning department, planning the processes involved in handling high-voltage systems. "I take care of the equipment, the system technology, and the production processes. I must ensure that all employees are protected in the best way possible when working with high currents and voltages."
His innovations are becoming the blueprint for other plants. "A comparable production facility is currently being set up in China, where our results will also have an impact." Working on the new Audi Q6 e-tron makes him proud. "This is the beginning of a new era. We all feel a certain hunger to get started now."
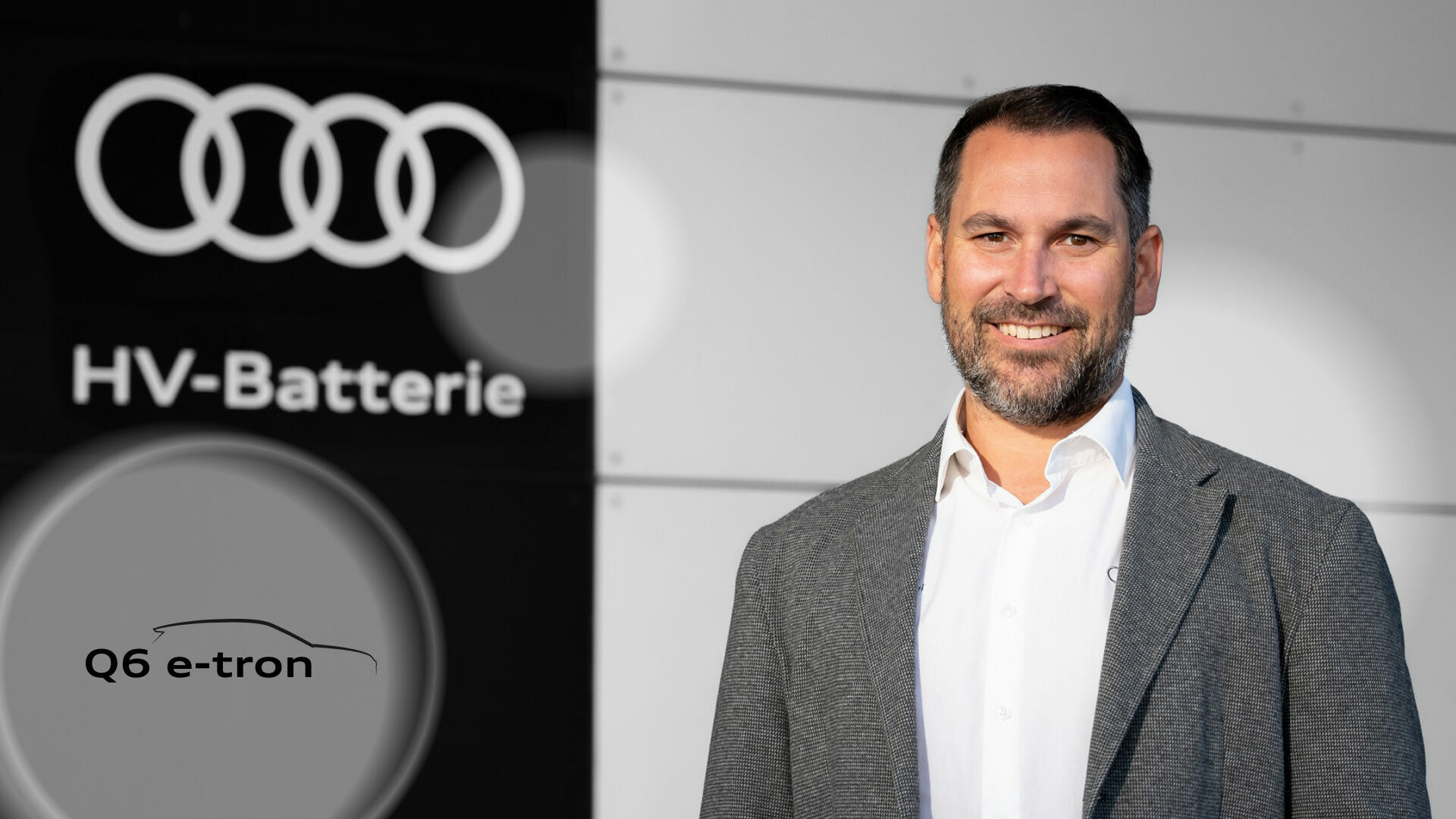
Sebastian Frei heads up high-voltage battery planning at Audi
Pioneering spirit and the best of all worlds: Sebastian Frei has formed a team of around 60 people for high-voltage battery planning in Ingolstadt, most of whom have come together internally and gained further qualifications. "Many had to jump in at the deep end - including us. We had to set up a new, individual qualification program for our employees - and we are still learning," says Frei.
Alongside his team, he puts his body and soul into the heart of the Audi Q6 e-tron: the battery. Other projects will soon follow. For example, the latest findings are in demand when setting up battery production facilities at other locations. Knowledge is exchanged throughout the Group and in both directions. "We are investing in the future here," says Frei, who believes battery planning is "one of the most attractive jobs at Audi.”